How Can Injection Moulding be Greener?
With the government committing to cutting the UK’s emissions by 78% by 2035 in an attempt to reach the net-zero carbon target by 2050, living greener and more sustainably is a hot topic.
Plastic injection moulding is a process that has gained a bad reputation for its green standards, and many think that the two could never go hand in hand. But that’s where you are wrong - at TCB-Arrow we are committed to ensuring our products and processes are greener, and we do so in a number of ways.
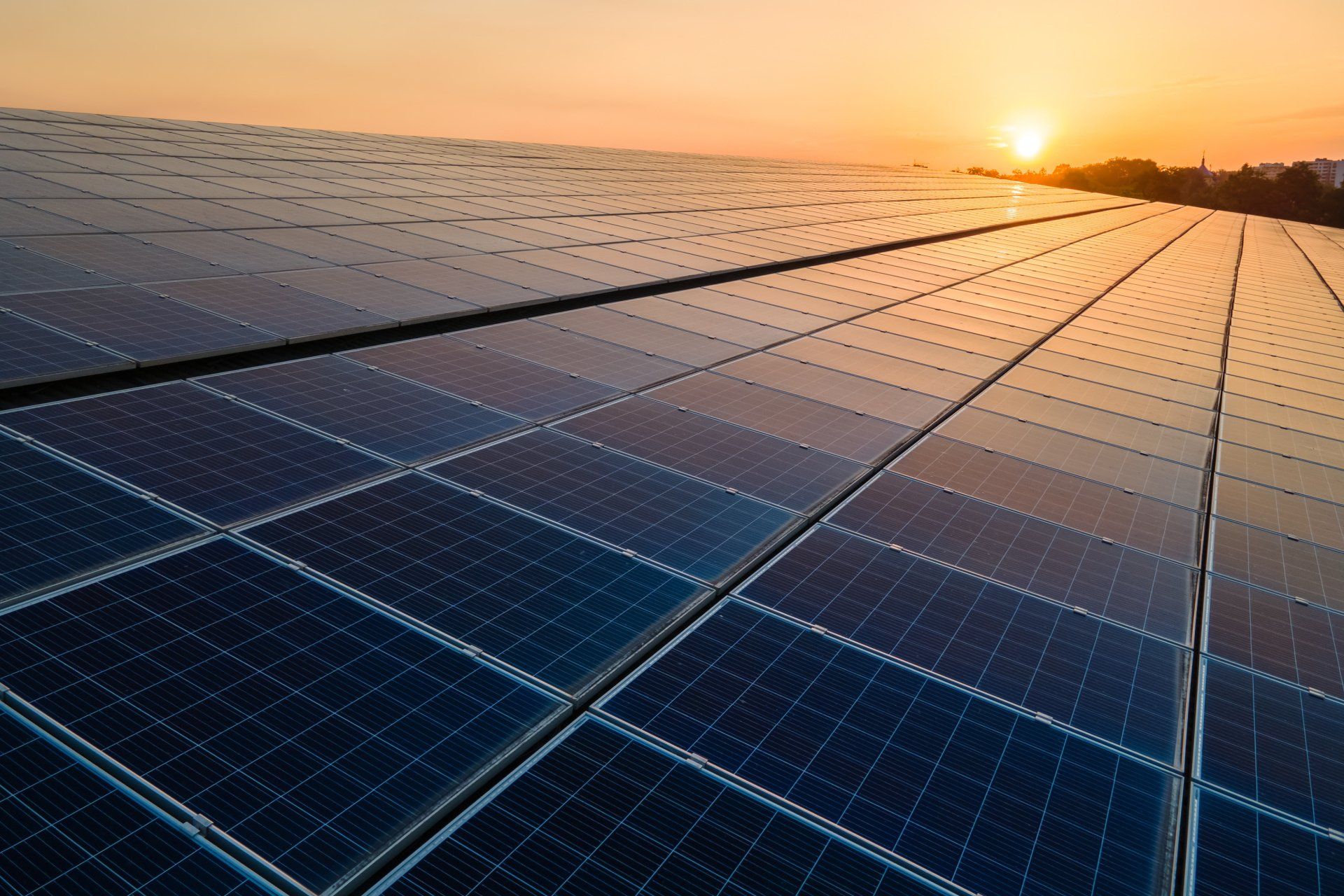
Design
We assist customers with the design of products in order to optimise the item's physical properties and material content, ensuring the material content is as economical as possible. This is achieved by making sure the section thicknesses of the part provides the necessary strength while not being too thick. If parts are made too thick, they take longer to cool, meaning the cycle time is longer and the production process is not optimised.
Materials
Not only do we evaluate the amount of material used, but also the ratio of Prime (new) to Reprocessed material. We try to use environmentally friendly materials for our projects where possible, with higher reprocessed content. Over 50% of the materials we use are reprocessed grades, which equates to over 30 tonnes a month.
Manufacturing Process
Aside from the materials themselves, the process of injection moulding is inherently low waste, and at TCB Arrow we have optimised our processes to reduce waste and improve efficiencies. By operating more efficient processes, cycle times are reduced, which in turn reduces direct energy cost per component, leading to higher output with less consumed energy. Current injection moulding machines are more environmentally friendly, so we regularly replace machines with the latest energy-efficient equivalents, to ensure we are producing with the least CO2 impact possible.
Optimising Our Factory
In terms of the space we operate in, we are doing all we can to ensure we are as environmentally friendly as possible. We operate a 24-hour shift system, meaning we can keep our machines running constantly, reducing any downtime and contributing to our high efficiencies. We are very conscious of the source of our electric supply and we endeavour to source our power from suppliers with a high sustainability content.
We are also aiming to become more self-sufficient, producing our own energy through solar PV panels. With this £100,000 investment, we expect to see a full ROI within 5 years due to the amount of energy saved and instead produced through our own solar energy.
Having been established for 35 years, at TCB-Arrow we have come a long way in terms of improvements in our environmental footprint and commitment to minimising the impact of our activities. It is our environmental consciousness that drives us to continually review and reduce our ecological footprint, and these are just some of the ways we are currently striving to do that.
We are a modern organisation providing components and assembly solutions in Thermoplastic and Elastomer materials. Visit our website to find out more.
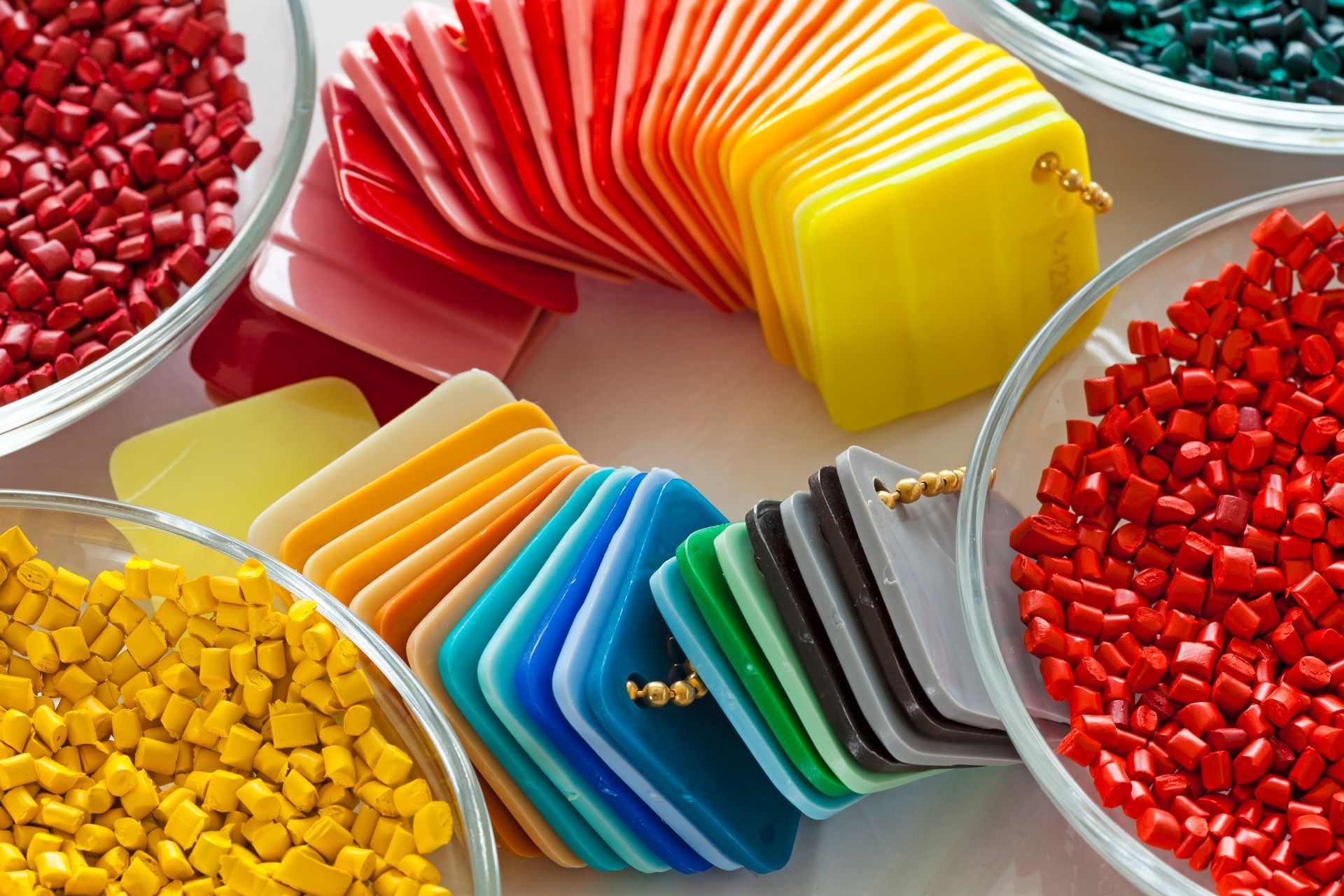
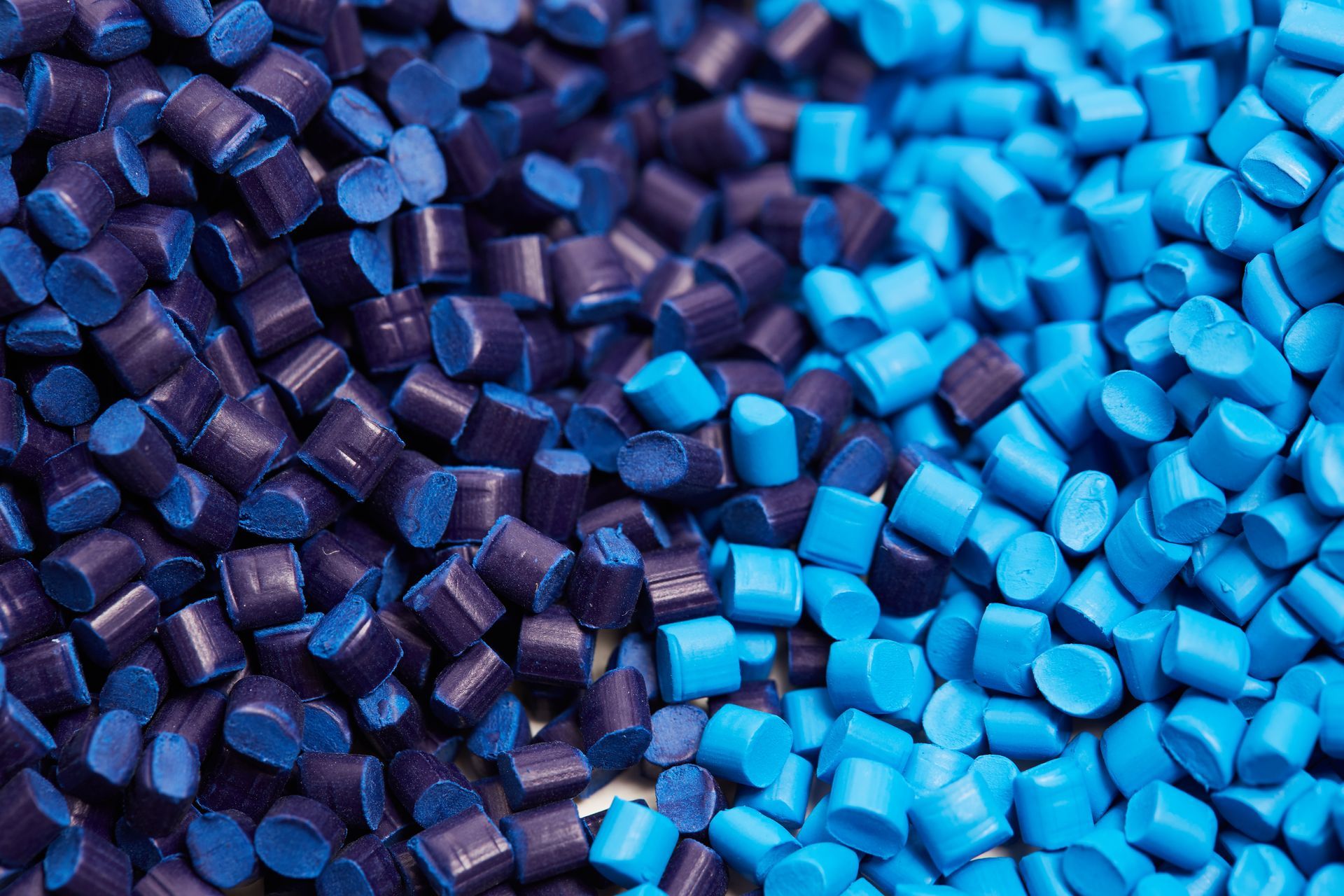