The Advantages and Disadvantages of Injection Moulding
Injection moulding is the recognised process for mass-producing identical plastic products. However, like all the other processes out there, there are many different factors to consider when deciding which is best.
AT TCB Arrow, we’re proud to say we have 35 years of experience in moulded plastics, so we’re familiar with the benefits of each. Here are some for you to consider to help inform your decision:
Advantages of Injection Moulding
- It Generates Less Waste - As the only plastic required for this process is forced into a mould, this is naturally a low-waste method of production. If this goes alongside a thoughtful approach to product design and energy-efficient production, injection moulding can lead to a much greener manufacturing process .
- Fast Production & Highly Efficient - Injection moulding can produce a very large amount of parts per hour. Depending on the size and complexity of the mould, typically cycle times can vary between 10-60 seconds.
- High-Output Production - The speed and efficiency of production means that thousands of parts can be produced before the tooling requires any maintenance. If the demand for a product is high, multiple cavities can be introduced to a tool. This means that, with each cycle, multiple of the same parts are produced.
- Quality Consistency
- Due to the repetitive nature of injection moulding, all parts produced will be identical. This means that you can rely on
high-quality parts being produced en masse.
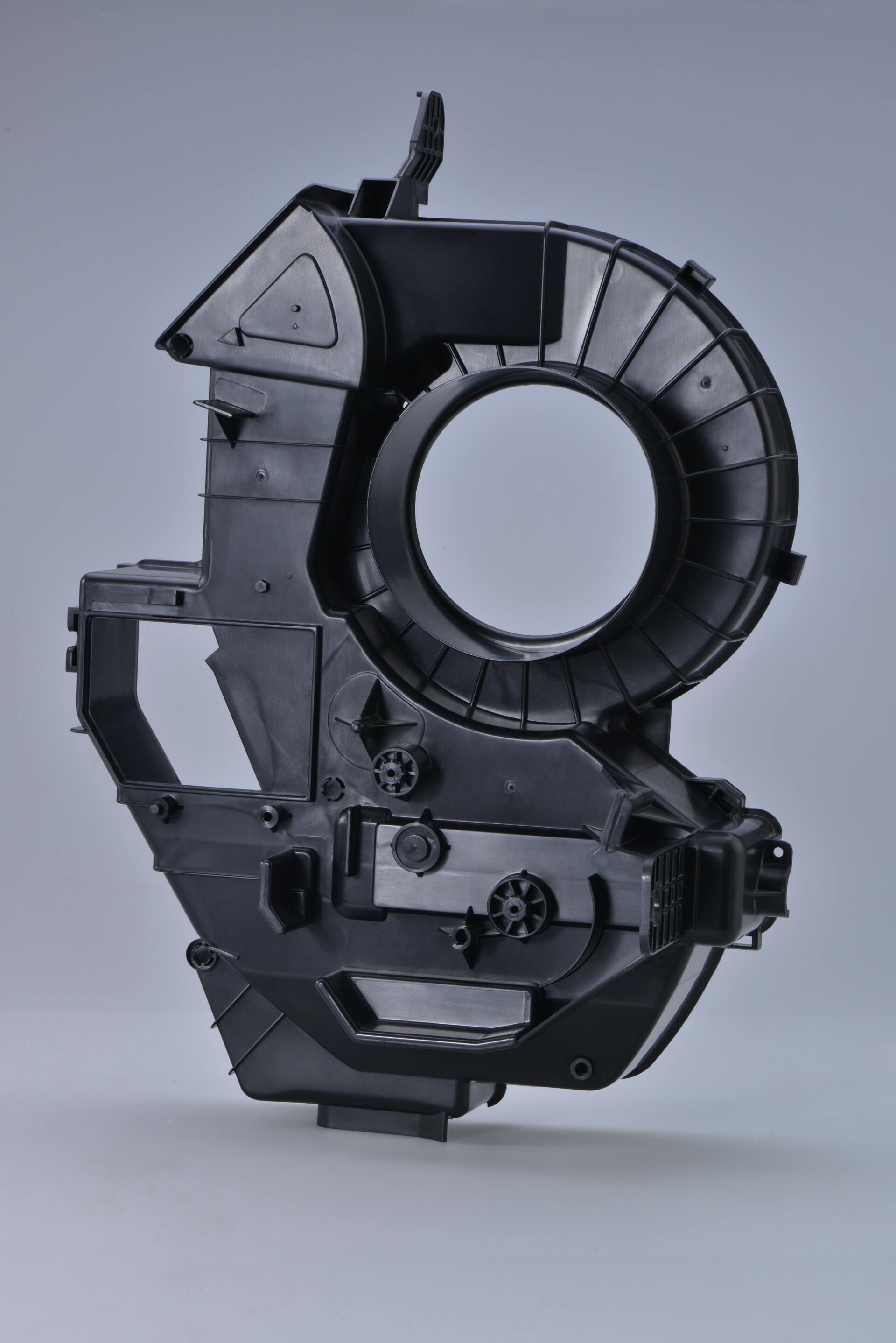
Disadvantages of Injection Moulding
- Restrictions of Part Design - Injection moulding requires certain regulations, and therefore there are some basic rules to follow when designing the plastic parts you plan to manufacture. Some examples of these are:
- Avoid sharp edges and undercuts as much as possible
- Make sure the wall thickness is uniform in order to prevent inconsistencies in the cooling process
- It’s encouraged that you use draft angles as these are better for demoulding
- High Tooling Costs - Because injection moulding requires design followed by the manufacturing of the tooling, the up-front costs of the process are high. However, this can be viewed as an investment when weighed against the low production cost.
- The Higher The Quantities, The Greater The Benefit - These higher startup costs mean that the process favours high quantities, so if a part you require isn’t in high demand then injection moulding can become a less attractive method. .
- Manufacturing A Tool Can Take Time
- The initial tooling manufacture does take time which means that the lead times on the first production run can be
elongated. This is counteracted when commencing future production runs as once the tool is made the production process is streamlined.
So, there you have some of the advantages and disadvantages of injection moulding. As a greener, more reliable and consistent method of manufacturing, it really is a great way to produce cost-effective and high-quality parts.
At TCB-Arrow, we pride ourselves on our process. We have the knowledge and facilities to help guide our customers through the design, tooling and mass production of their plastic products.
Contact our helpful team to find out more.
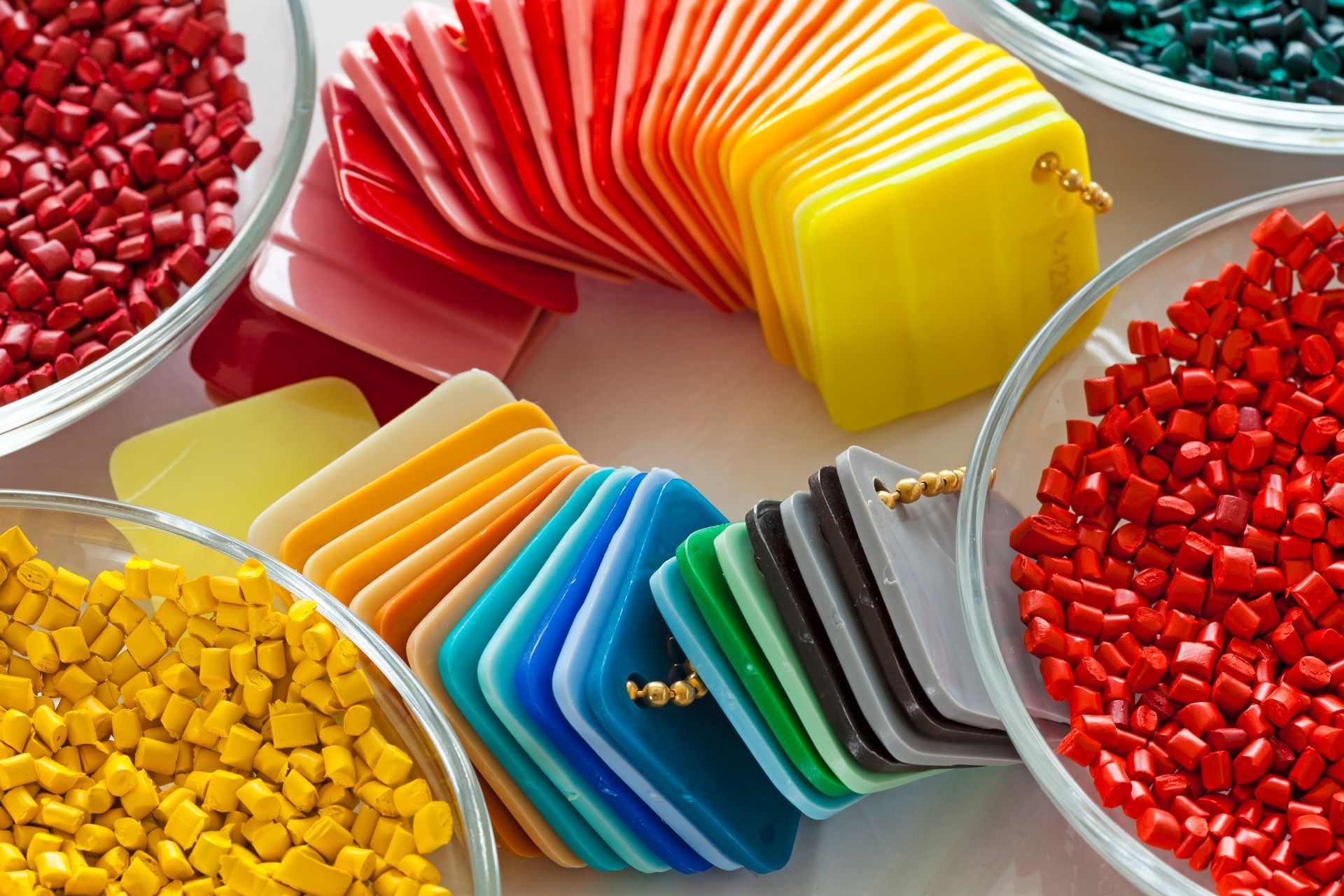
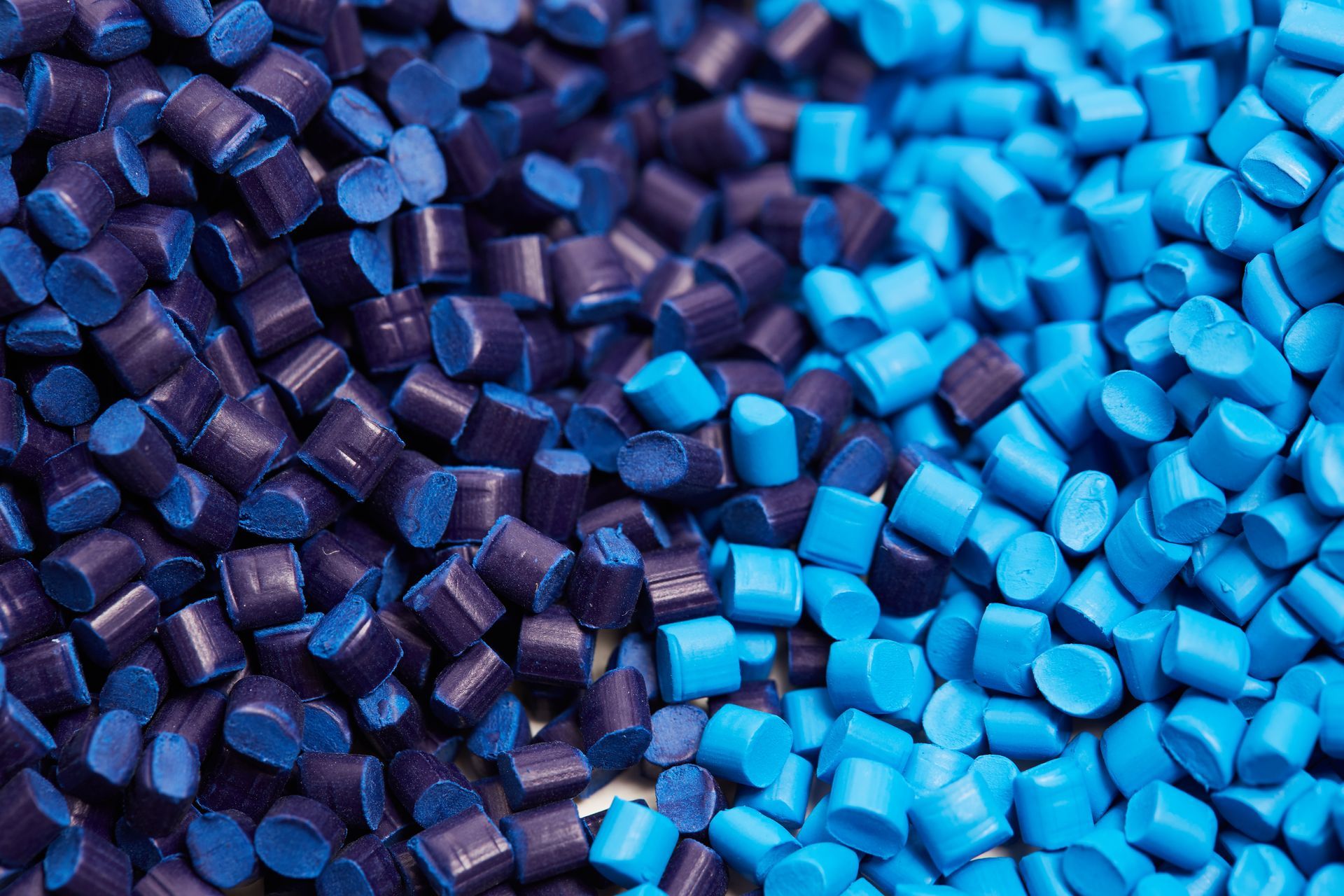