How TCB-Arrow Works with Optical Liquid Silicone Rubber
Due to its extensive list of beneficial properties, Optical Liquid Silicone Rubber (or OLSR) is becoming hugely popular in the Lighting and Medical markets. From wearable technologies and endoscopes to light guides and medical lasers, Optical LSR combines high-clarity optical qualities with the adaptable nature of polymer-based materials.
But what are these characteristics that make it so desirable? And how do all of these factor into production? Well, OLSR can come with some very specific challenges, which means a lot of facilities avoid it altogether. In this article, we’ll go through all the benefits of OLSR and how TCB-Arrow is equipped to handle its obstacles.
The Benefits of Optical Liquid Silicone Rubber
What makes OLSR unique is that it carries the optical clarity (transparency) of materials such as glass and Polycarbonate, with the incredible versatility of a silicone-based material. This versatility has led to its use in some groundbreaking applications.
It has incredible heat and UV resistance, meaning it won’t yellow over time or break down after long periods of thermal exposure. This makes OLSR ideal for light fixtures as well as a variety of
medical applications, where glass or polycarbonate may fall short.
Furthermore, it’s extremely hard-wearing, scratch-proof and has high light transmission, making it ideal for a wide range of applications and increasing its demand. But what challenges does this bring?
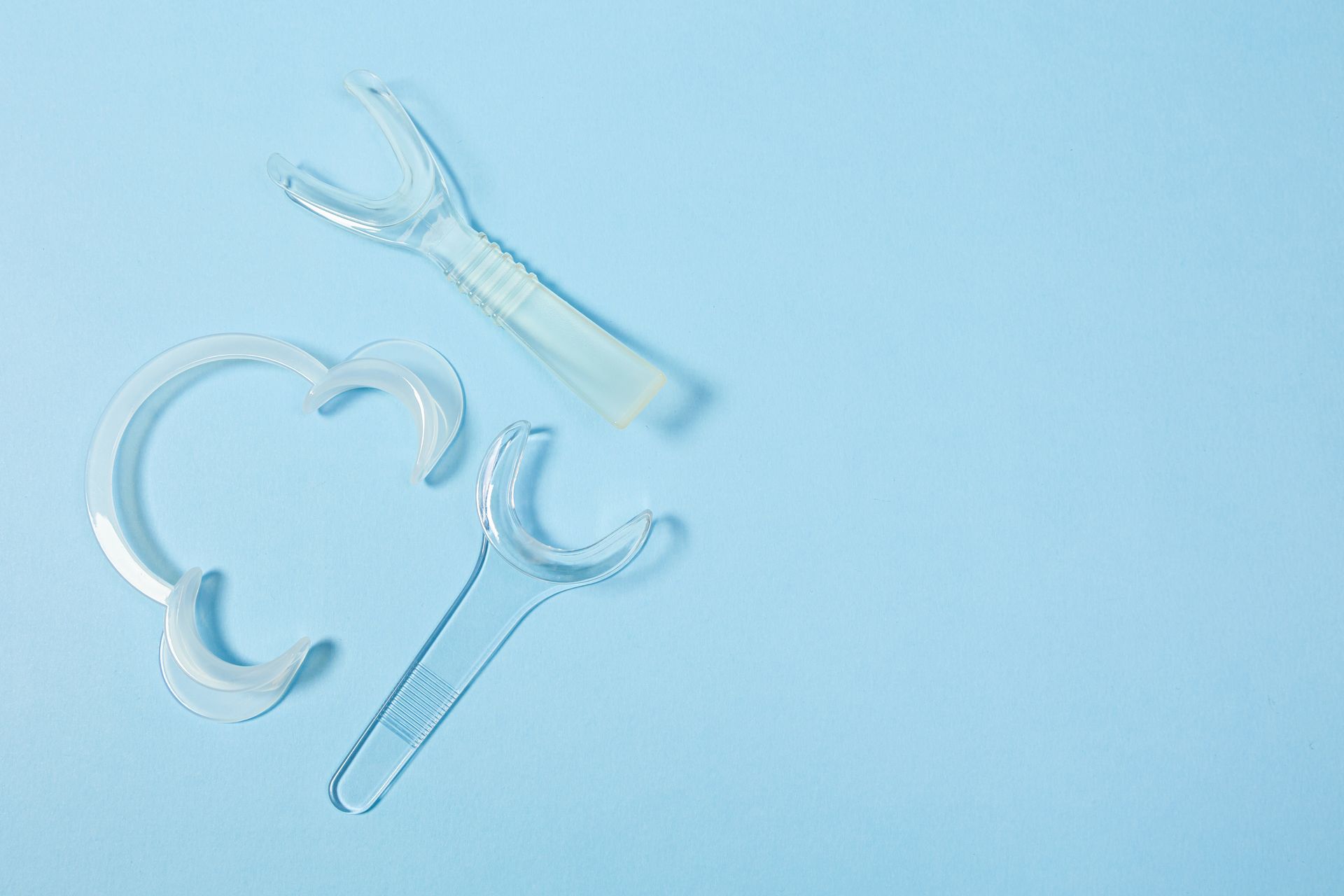
Considerations when Injection Moulding Optical Liquid Silicone:
Contamination
Due to the unique applications of OLSR, contamination can negatively affect the transparency of the component, or in some cases, it can make the component unsuitable for medical use.
One cause of contamination can occur when optical grade silicone mixes with a standard silicone whilst being processed. This can cause a murky effect within the components where the visible difference in material grade can be seen. Therefore, making sure that the mixing and metering pump is only used for that specific grade of material is critical to producing good parts.
Another form of contamination happens when particles from the environment stick to the components after they have been produced. To combat this, our team at
TCB-Arrow uses ionising air blowers to remove the static charge of the components and prevent any external contamination of the parts.
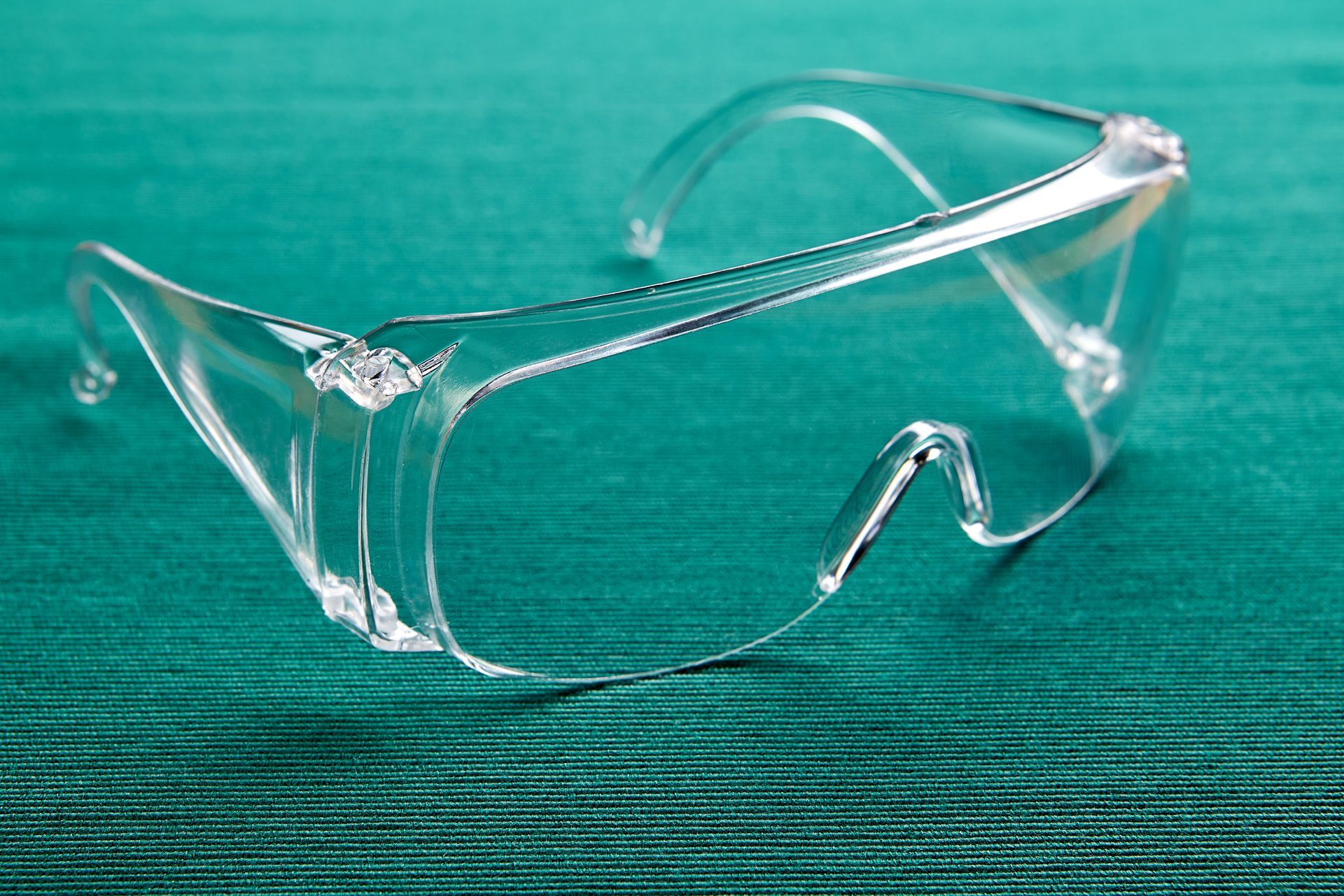
Process Considerations
When being used for lighting applications, OLSR products must be fully formed and made to the correct dimensions, as any errors will affect the path of the light and could result in an inefficient light source.
To avoid this, the OLSR Injection Moulding machine must be
tested regularly to ensure that the process is stable and that there has been absolutely no deviation from the parameters that have been set.
Mould and Part Design Considerations
Due to the fact that OLSR reproduces every aspect of the mould surface, any surface imperfections on the mould must be eliminated before the process begins. In addition to good surface quality, this is a critical step when injection moulding OLSR to improve the refractive index of the product.
Additionally, although the mould design conditions for liquid silicone rubber suggest that the parting line would cross over with the venting areas, it’s recommended that the venting zones for OLSR be on the upper part of the mould. This is due to the low viscosity of the resin.
Contrastingly, the advantage of Optical Liquid Silicone Rubber’s lower viscosity is its ability to reach thin areas of moulds and fill very small cavities, giving the product designer a greater amount of freedom when creating fine features, whilst also allowing for thinner walls on the product.
All of this requires a lot of planning and attention to detail, which is something that we have decades of experience with at TCB-Arrow. Although OLSR has a lot of specific requirements, our team is prepared to meet them–from design all the way through to manufacturing. Get in touch with our team to find out more.
At TCB-Arrow, we pride ourselves on our process. We have the knowledge and facilities to help guide our customers through the design, tooling and mass production of their plastic products.
Contact our helpful team to find out more.
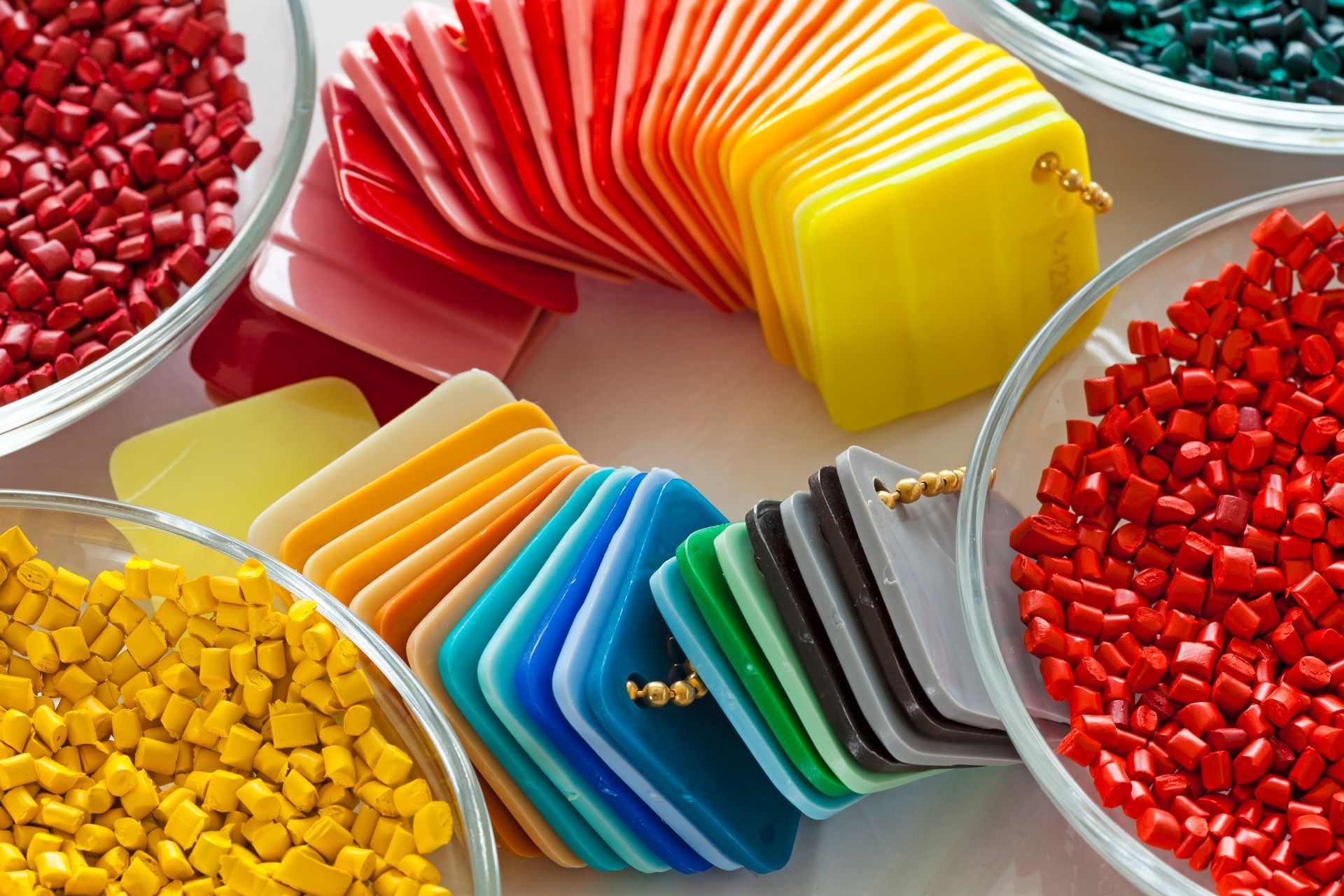
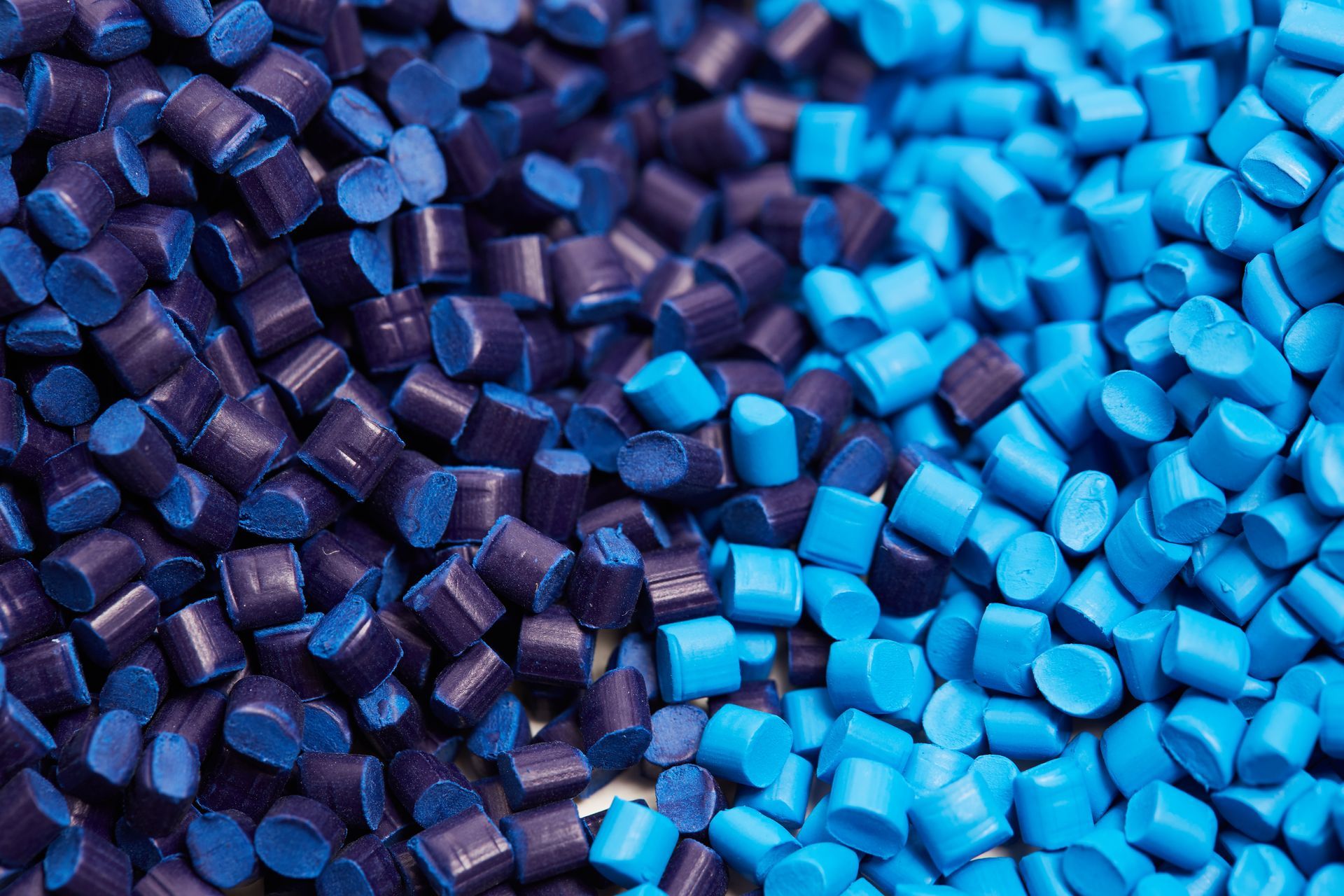