3 Helpful Additives That Make Your Plastic go Further
Plastics are an essential material for manufacturing millions of parts, components and products across the world each year. Sometimes the properties and behaviours need to be formulated in order to serve the right purpose.
This is made possible by introducing additives, which enhance certain properties and help to deliver the desired outcomes to the plastics with which they’re combined. Here are three popular additives which serve different purposes in plastic production:
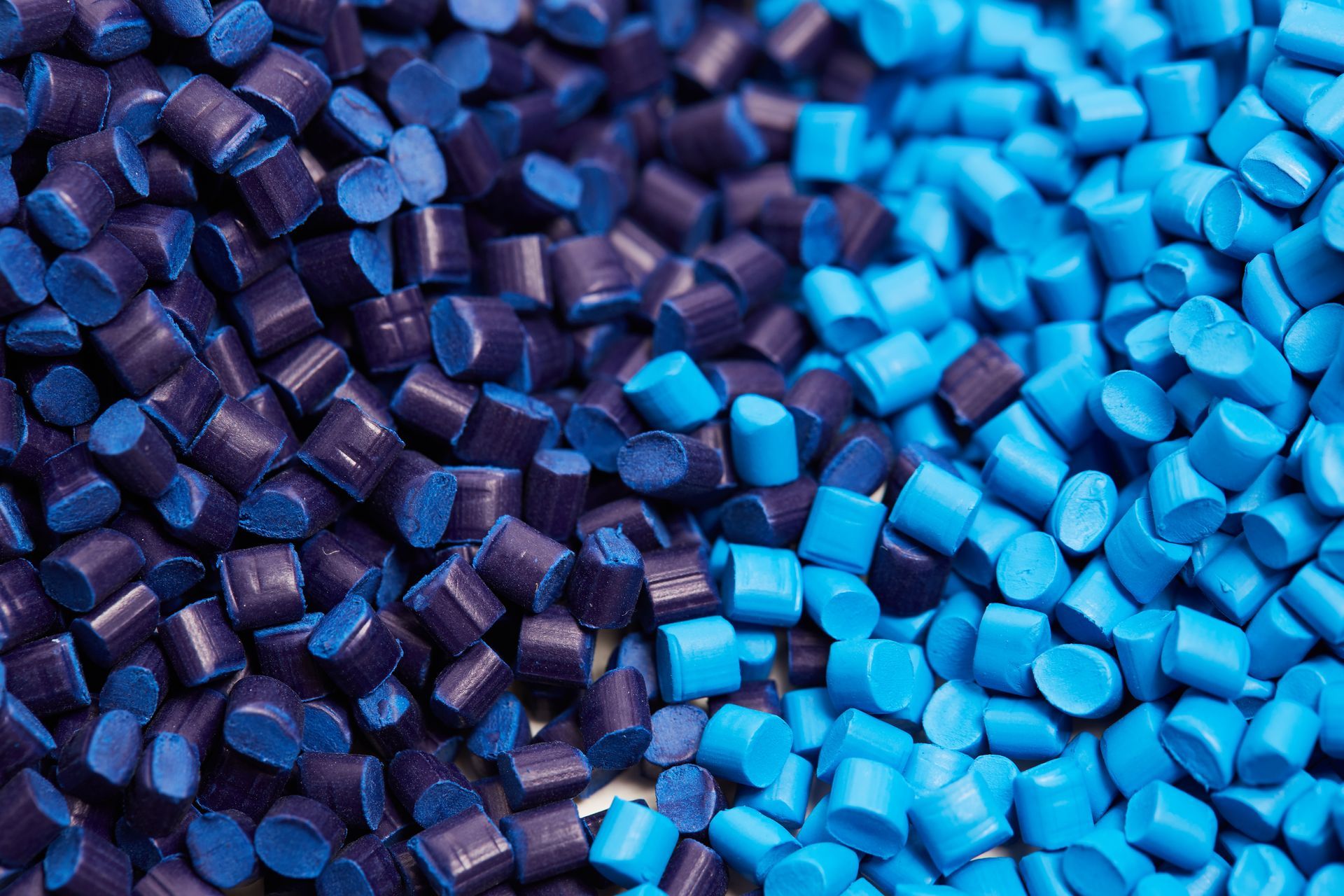
1. Glass Fibres
Glass fibres are very commonly used in the injection moulding process, as they can significantly improve the rigidity and strength of plastics, helping them to become more robust and resistant to stress cracking.
However, this rigidity also can make plastics more brittle. This means that glass fibres are a great additive for parts that won’t be exposed to a lot of high-impact stress and will have a fairly stable purpose, but not those which endure a lot of pressure or defection.
2. Masterbatches (Colourants)
In order to colour the raw polymers of thermoplastics in the most cost-effective way, masterbatches are added to them at 2%. These are beneficial as they dilute well, allowing for higher levels of accuracy when dosing expensive components.
Another positive aspect of using masterbatches is the fact that they can improve product consistency, as they disperse well and therefore allow for more process stability.
3. Talc
Talc is commonly used in polymer compounds, as its fine particles effectively fill up the inter-particular spaces to increase their stiffness and impact strength. It also provides higher levels of thermal conductivity, which means that the process of heating and cooling plastic compounds becomes quicker. In turn, this then leads to faster production rates.
Talc achieves the highest creep resistance against any other mineral filler, as well as having the lowest hygroscopicity of powdery fillers. This means that it will not take on a high percentage of atmospheric moisture however, in some cases it may still need to be dried before it can be processed.
As each has its own unique set of properties and benefits, the use of any of these three additives in the injection moulding process can help to produce the desired outcome for your plastic part. These are just three of many additives that we use at TCB-Arrow, as we have experience in creating plastics for a wide range of applications.
At TCB-Arrow, we have over 35 years of experience in selecting, applying and combining the right additives to achieve the perfect plastic products for our customers. Get in touch with our helpful team to find out more.
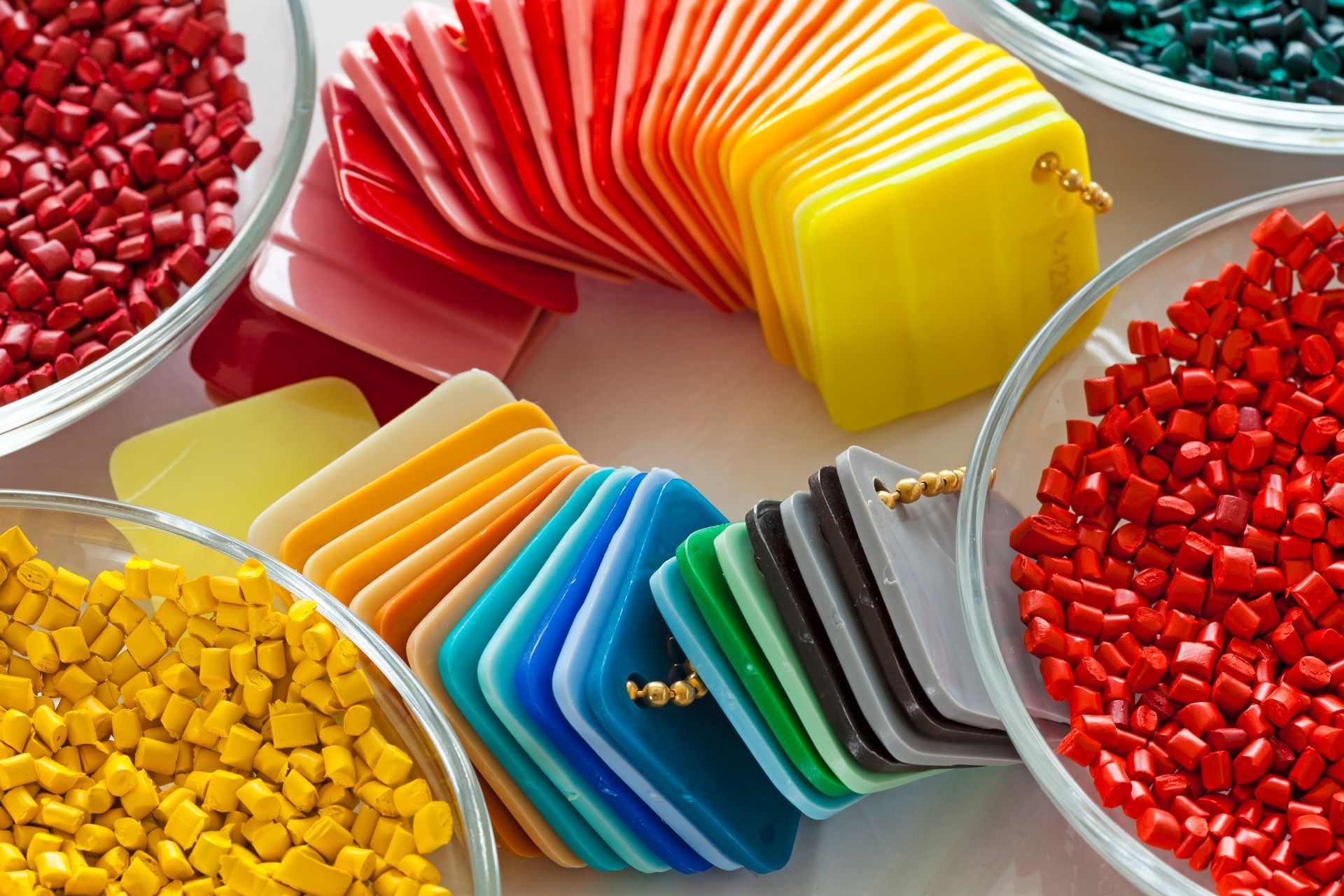