3 New Krauss Maffei Machines for 2018
In line with our continued investment plans we have just taken delivery of 3 new Injection moulding Machines to complement our existing equipment. These consist of a 130 tonne and two 80 tonne Krauss Maffei machines. In the last 3 years we have invested over £500k in new plant and equipment, demonstrating our continued commitment to our business and customers.
Efficiency
With Servo driven Hydraulic pumps on all 3 machines, we expect to see a 40% energy saving over older machines. This is not only in line with our environmental policy and objectives, but it provides a real commercial saving that we will pass onto our customers putting us at a competitive advantage.
Control and Repeatability
These new machines are very accurate in operation. Injection volumes and speeds are so accurately controlled that we are able to achieve injection times between shots that are consistent to within 0.01 seconds. Combining this with very accurate injection volumes through screw positions measured to 0.01mm, we achieve excellent repeatability between cycles. All of the variable settings are saved in the machine SSDs or on USB sticks; these can then be shared between machines, ensuring that jobs can be put up and repeated accurately from batch to batch, also saving valuable setup time.
Quality Control and Validation
With many of our customers requiring process validation studies to be performed, we comfortably achieve these tight validations through machine accuracy and repeatability. We work to FDA process validation formats, conducting Installation, Operational and Production Qualification Validations (IQ, OQ & PQ). Within these studies we output a measurement of process stability that takes 3 standard deviations of the measured critical dimensions and weights - it then applies these to tolerances that are generally tightened considerably up on those defined by the customer. Once we have approved the process then we set Quality Parameters on the moulding machines to ensure that any slip in the process causes the machine to alarm well before unacceptable parts are produced.
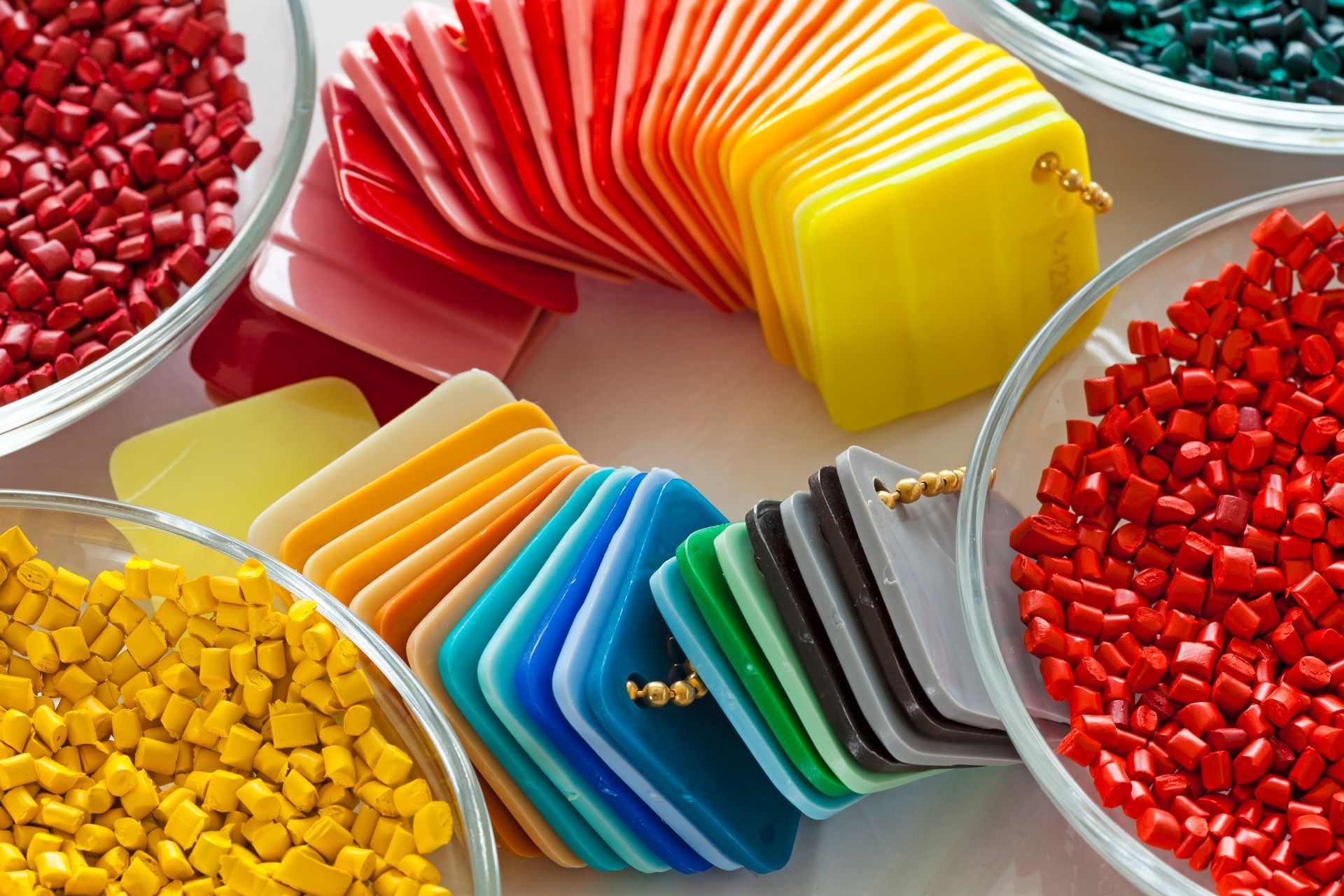
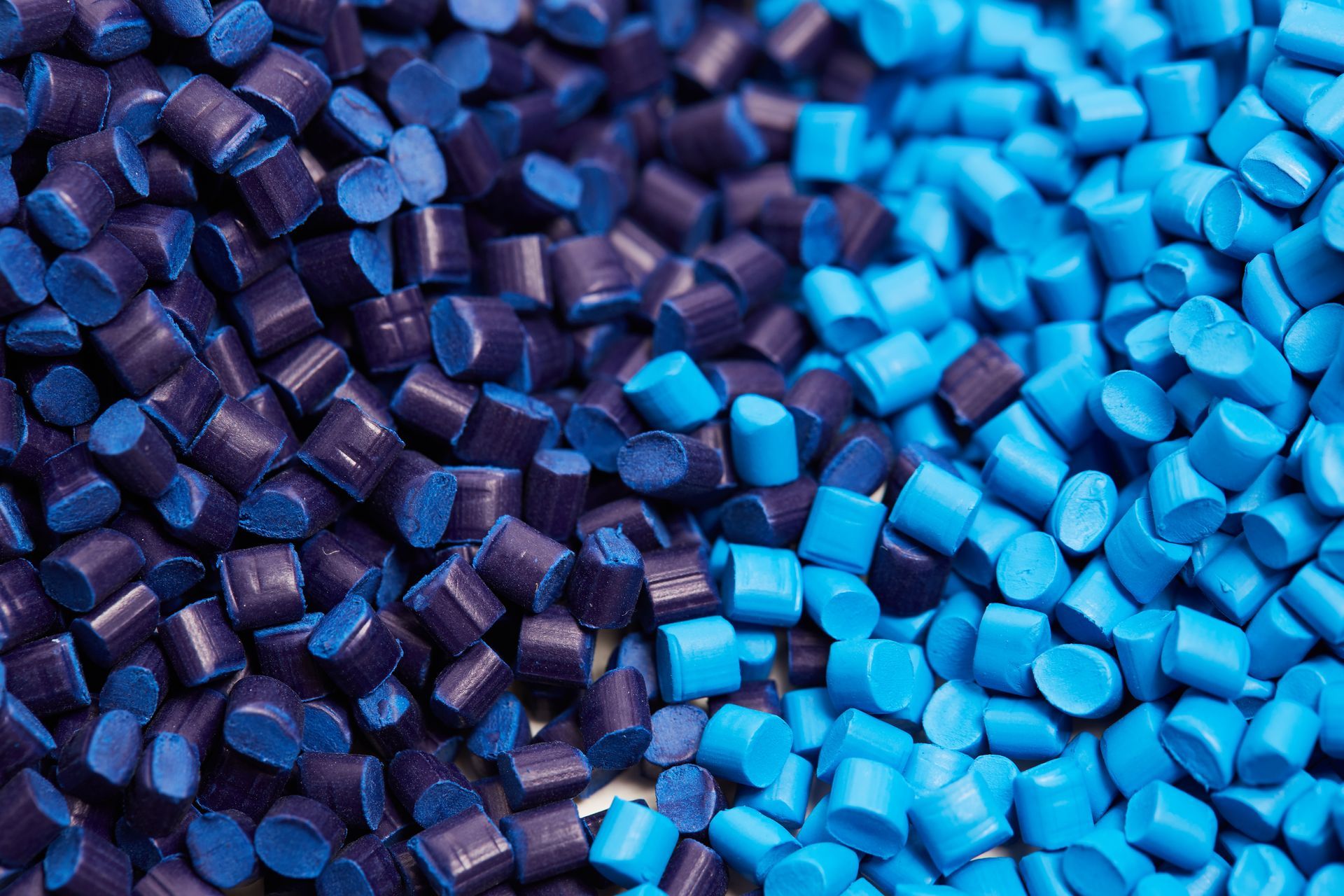