What are Design For Manufacturability (DFM) Reviews and Why are they Important?
DFM is an engineering review to evaluate the manufacturing feasibility of a product design along with addressing and highlighting any manufacturing concerns that might be evident from the design prior to proceeding with tooling.
During this review phase there is also a potential opportunity to reduce manufacturing costs by illustrating the general tool layout and highlighting any complex/costly tooling ancillaries i.e. side actions, mould lifters etc that are required to achieve the level of design being analysed. The customer then has the opportunity to adjust their design to negate the need for these ancillaries which in turn can help reduce overall manufacturing costs. The DFM Review is the most informative and efficient method of evaluating any part design prior to tool manufacture. At TCB-Arrow the DFM Review is a key stage in our New Product Introduction (NPI) Process.
In general, there are many critical aspects of a part design that are reviewed during a DFM. These are as follows:
- Suitable materials to consider for the part application and their applicable mould shrinkage allowances
- Tool/part split line positions
- Optimum gate feed position and type
- Ejection style and positions
- Wall section thicknesses
- Potential levels of distortion and sink
- Draft angle and venting recommendations where required
- Surface finishes
- Part tolerances and areas to leave “metal safe” for dimensional adjustments once tool manufactured.
These are just some of the key points covered during our reviews.
To help illustrate these points please see below a selection of pages from a few of our DFM first stage reviews for parts to be manufactured at TCB-Arrow:
In conjunction with any DFM review an Advanced Moldflow Analysis can also be undertaken to help optimise a part design. These types of analysis are often performed if there are:
- Part material selection issues
- Thickness / Thinness problems
- Structural concerns, for weld line controls, residual or structural stress issues
- Filling concerns
- Product function requirements
- Sink or appearance concerns
- Cooling channel optimisation for reduced production cycle times and distortion
To help illustrate this type of analysis please see below a selection of pages from a typical TCB-Arrow Mouldflow Analysis:
In summary, both DFM & Moldflow Studies are very useful tools to assist in identifying aspects of a part design that are likely to be problematic at the moulding stage. These reviews provide the opportunity to make the necessary changes in tooling and part design to prevent moulding issues.
Please don't hesitate to get in touchwith our expert team on +44 (0)1276 679394 for more information on how we could facilitate your project.
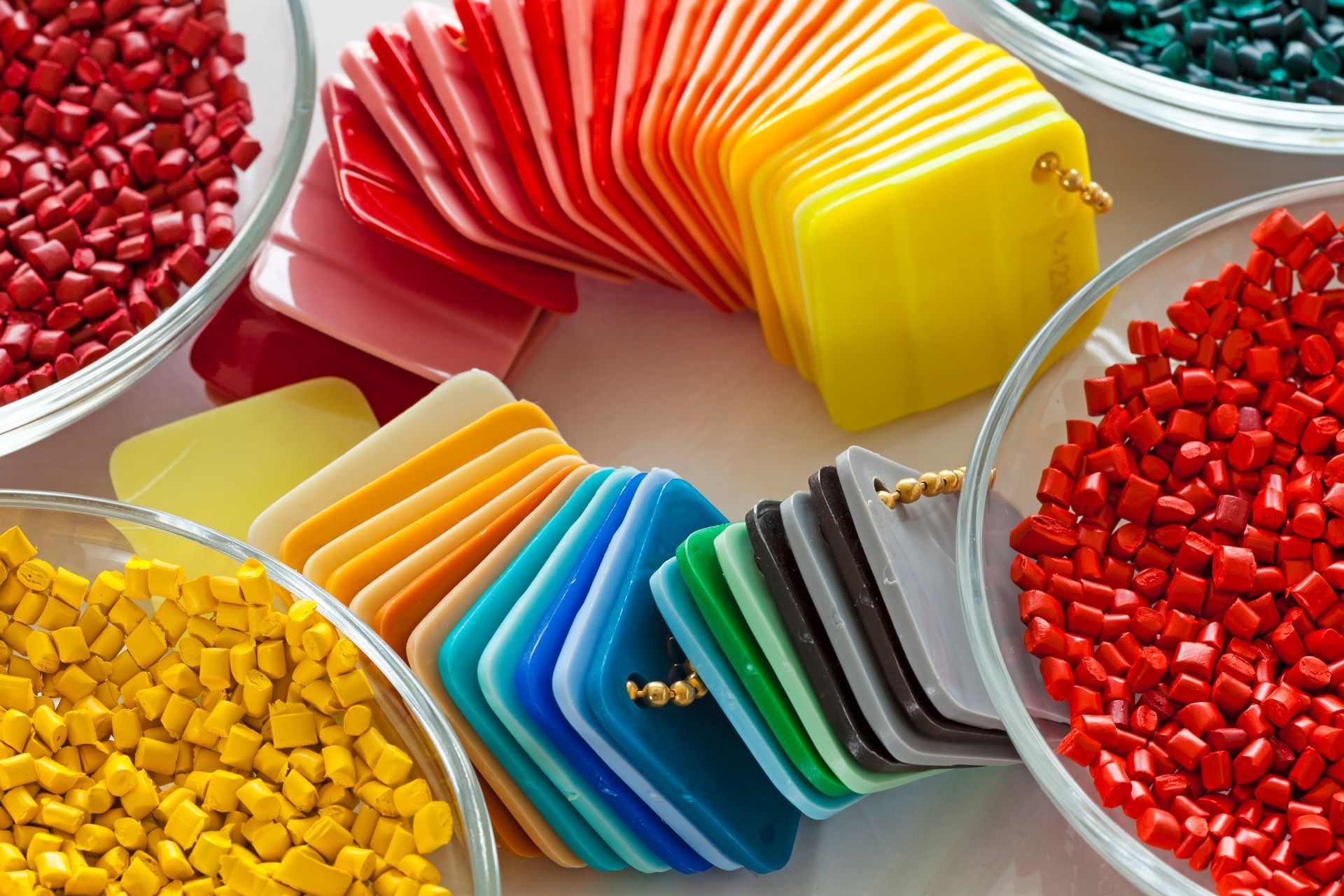
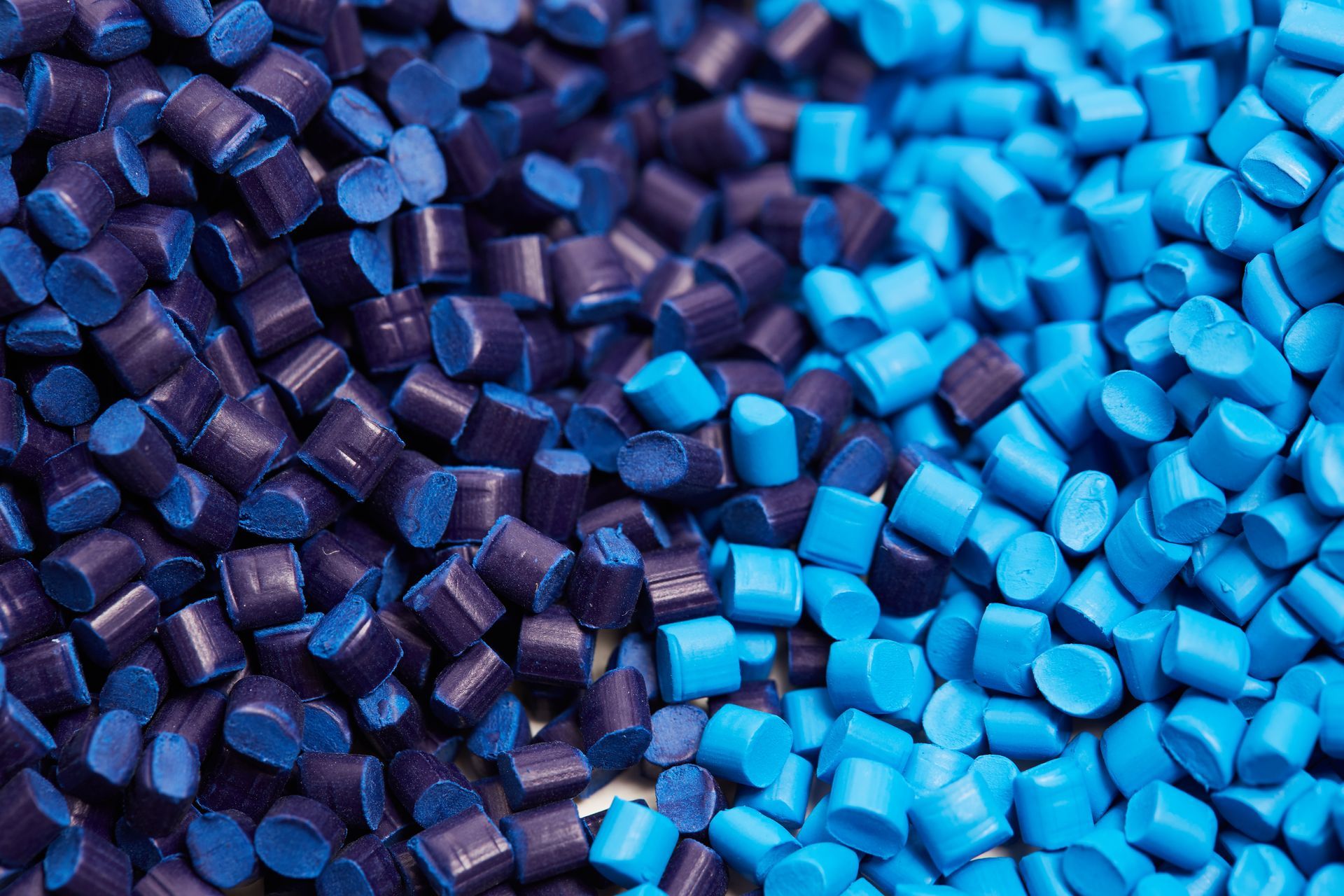